Best Pneumatic conveying Company - Allway
Allway Best Pneumatic conveying Company - Allway,We can not only customize or batch customize a single material unloading or conveying products, more committed to the production of complete sets of material unloading, conveying, storage, weighing, mixing and screening, packaging and other systematic product equipment.
Pneumatic conveying is an important part of clean production, it is the use of air (or other gas) flow as conveying power, in the pipeline to carry powdered solid materials. The flow state of the material in the pipeline is very complex, depending on the solid to gas ratio of the material in the pipeline are dense phase conveying system. Pneumatic conveying systems are widely used in petroleum, chemical, metallurgy, building materials, grain and oil, pharmaceutical and other factories for the conveying of some raw materials, powder and granular materials.
Materials that can be conveyed by pneumatic conveying system.
Pigments, dyes, paints, carbon black, titanium white raw materials, iron oxide, ceramic powder, heavy calcium, light calcium, bentonite, molecular sieve, kaolin, silica gel powder, activated carbon, urea, ammonium chloride, ammonium bicarbonate, soda powder, solid pesticides, tungsten powder, pesticide additives, copper concentrate powder, coal powder, phosphate ore powder, alumina powder, cement, clay, yellow sand, quartz sand, clay powder, silica, limestone powder, wood chip powder, glass fibre, silica, flour, starch, grains, milk powder, food additives, etc.

Classification.
(1) According to the characteristics of the conveying device, pneumatic conveying can be divided into negative pressure conveying, positive pressure conveying and mixed conveying.
(a) Negative pressure conveying
Negative pressure conveying system is also called suction conveying. It is powered by the negative pressure formed when the air-entraining device at the end of the conveying system is in operation and the pressure difference between the outside world. Due to the existence of the pressure difference, the outside air is sucked into the pipe, while the material is brought into the pipe with the movement of the air. After reaching the end, the material is separated from the air and collected, while the air is purified and discharged into the atmosphere or recycled. Negative pressure conveying systems are mostly used for centralised conveying,that is conveying from multiple points to one point, such as dust removal in workshops, grain into silos, etc. The advantage of negative pressure conveying is that it can effectively collect the material, the material will not enter the atmosphere, which is especially important for the pneumatic conveying of toxic materials, but due to the influence of vacuum, its conveying distance is limited to a certain extent, the general system pressure drop limit is O.044MPaf71.
(b) Positive pressure conveying
Positive pressure conveying, also known as pressurised conveying, is the earliest pneumatic conveying system in use and the most basic form of pneumatic conveying. Positive pressure conveying is the use of the fan at the beginning of the system to the conveying pipeline into the compressed air, the use of the beginning of the pipeline and the end of the pressure difference, so that the air flow in the pipeline, and drive the material movement. In the positive pressure conveying system, the material is fed into the conveying system by the feeding device and at the end of the conveying, the material is separated from the air. Compared with the negative pressure pneumatic conveying system, the conveying distance of the positive pressure conveying system is longer. The positive pressure conveying system is suitable for dispersed conveying, i.e. a point to multi-point conveying, in the conveying pipeline, the material can rely on the gravity of the material and the conveying medium to achieve separation in any discharge point.
(c) Mixing and conveying system
Mixing and conveying system is in the same conveying system will be positive pressure conveying system and negative pressure conveying system joint use of a conveying system. The hybrid conveying system combines the characteristics of both positive and negative pressure conveying systems and can therefore be used for complex conveying conditions.
The advantages and disadvantages of negative pressure conveying, positive pressure conveying (low-pressure, high-pressure and mixed conveying) are compared and analysed in relation to the applicable occasions.
Negative pressure conveying.
1. easy to pick up material, suitable for the occasion that requires no dust to be produced.
2. Suitable for low, deep or narrow pick-up points and for concentrated feeding from several places to one.
3. as the air source is located at the far end of the system, lubricating oil or moisture will not be mixed with the material being conveyed, thus avoiding moisture, dirt or other debris in the material and ensuring the quality of the material being conveyed.
4. because the pressure inside the conveying tube system is lower than the atmospheric pressure, so even if wear and tear occurs and there is a gap, the conveyed material will not leak out.
5. Because the pressure inside the conveying system is lower than the atmospheric pressure, the moisture is easy to evaporate, so it is easier to convey the materials with more moisture than the pressure feeding type.
6. the addition of dust filter at the inlet end can adopt clean gas general working vacuum is less than 0.08Mpa, so the conveying volume and conveying distance cannot take large values at the same time.
7. the conveying pipeline can be flexibly arranged, so that the plant equipment process configuration is reasonable.
8. the realisation of bulk material conveying, high efficiency, reduced packaging and handling transport costs
9. few moving parts, easy maintenance and easy automation.
10. A variety of process operations can be realised in the conveying process, such as mixing, crushing, grading, drying, cooling, metering and dust removal
11. Negative pressure conveying system is mostly used for centralized conveying, i.e. multiple points to one point, such as workshop dust removal, grain into the warehouse, etc.
12. The advantage of negative pressure conveying is that it can effectively collect the materials and the materials will not enter the atmosphere, which is especially important for the pneumatic conveying of toxic materials.
13. For materials with unstable chemical properties, inert gas conveying can be used.
Disadvantages.
1. the need for good performance separation and dust removal equipment prior to the gas source.
2. the large size of the equipment due to the use of the gas source equipment for the suction of the expanded air
3. The standard star unloader under the separator tends to leak and cause irregularities in the system, so a pneumatic conveying rotary valve with good air tightness should be considered.
4. Due to the influence of vacuum, its conveying distance is limited to a certain extent, and the limit of general system pressure drop is O.044MPaf71
Scope of application.
1. taking material from silos, floors, centrifuges.
2. conveying in the food industry.
3. Conveying in the chemical industry.
4. Conveying in the pharmaceutical industry.
5. Conveying of toxic materials.
6. automatic conveying at the exit of silos
7. Bulk warehouse pick-up conveying.
8. Multi-point pick-up conveying.
9. open bag feeding station conveying.
10. A variety of upstream equipment discharge conveying.
Positive pressure conveying.
Low pressure positive pressure conveying
1. Suitable for decentralised conveying from one place to several places
2. Because the system is under positive pressure, there are no gaps, atmospheric or rainwater intrusion in the system components such as joints
3. Due to the positive pressure inside the system, the material is easily discharged from the discharge port
4. The temperature of the gas in the conveying process can dry the material
Disadvantages
1. the material supply is more difficult than the suction type, it should correspond to the physical properties of the material to be conveyed and the conveying parameters to select and design a suitable feeding device.
2. If the Roots fan is used as the air source, the pressure cannot reach very high, so the conveying volume and conveying distance cannot take large values at the same time.
Scope of application.
1.Chemical industry.
2. petrochemical industry (especially with nitrogen. Carbon dioxide gas conveying).
(3. Granular or flaky material conveying in the chemical or food industry).
High pressure positive pressure conveying
1. Conveying conditions can be achieved even if they vary due to the use of gas supply equipment with high exhaust pressure
2. High conveying efficiency due to adjustable mixing ratios in thin conveying tubes
3. Due to the small air volume required for conveying, the size of the structure of the separator and dust collector can be reduced
4.Conveying even in places where back pressure exists
5. It is possible to clean up residues in the pipeline
6. The end of the machine can be used for more than one material receiving point
7.The equipment is integral and easy to move. 1.The silo type is a closed pressure vessel, if it is used as a continuous conveying system, an intermediate storage hopper should be set up in front of the sending tank.
Disadvantages.
1. powder can be directly conveyed by pressure in the sending tank, but a rotary feed valve should be set in the upper part of the sending tank for coarse materials.
2. High air quality is required, no water should be contained.
Scope of application.
1. long distance and large capacity conveying (aluminium fluoride, fluorite powder, sodium fluoroaluminate, sand)
2. Feeding and conveying of high pressure containers (granular materials, powders).
Hybrid conveying
Combines the advantages of negative pressure conveying and positive pressure conveying and can be used for more complex working conditions. However, it has a high technical application and is mostly used for the mixing and drying of a variety of materials. Due to the complexity of the working conditions, the cost is higher.
(2) According to the material to gas ratio, the pneumatic conveying system can be divided into dilute phase pneumatic conveying, dense phase dynamic pressure pneumatic conveying, dense phase static pressure pneumatic conveying.
(a) Dilute phase pneumatic conveying
The dilute phase pneumatic conveying is characterised by high airflow velocity in the conveying system, the material is in suspension and the void rate is large. The conveying of materials mainly relies on the kinetic energy of the airflow velocity. The speed of dilute phase pneumatic conveying is usually 12~40m/s, and the mass ratio of material to gas is generally 1~5, with the maximum not exceeding 15.
(b) Dense phase dynamic pressure pneumatic conveying
Dense phase dynamic pressure pneumatic conveying airflow speed is generally between 8 ~ 15m / s. Dense phase dynamic pressure pneumatic conveying materials in the tube is dense state distribution, relying on the kinetic energy of the air to transport. These air conveying devices are: high pressure pressure conveying, high vacuum suction conveying and fluidised conveying. The material to gas ratio of Dense phase dynamic pressure pneumatic conveying varies greatly, the material to gas ratio of high-pressure pressure conveying and high vacuum suction conveying is roughly between 15 to 50, the flow state is pulsating group flow; and for easy to inflate the powder material, the material to gas ratio is up to 200 above, is fluidized conveying.
(c) Dense phase static pressure pneumatic conveying
In dense phase static pressure pneumatic conveying, the material is densely packed and bolted to the pipe, relying on the static pressure of the airflow to push the material. Dense phase static pressure pneumatic conveying can be divided into two kinds of column flow and bolted flow: column flow pneumatic conveying: dense material continuously filling the pipeline and the formation of material column, column movement speed is low, generally 0.2 - 2m / s, column flow pneumatic conveying is only suitable for short distance conveying. Bolt flow pneumatic conveying: artificially cut the material column into shorter material columns in advance, when conveying, the air bolts and material bolts are separated from each other. Pneumatic conveying is suitable for medium distance conveying.
This section is based on our existing information and our own experience, please contact us if any description is not in place, welcome your correction.
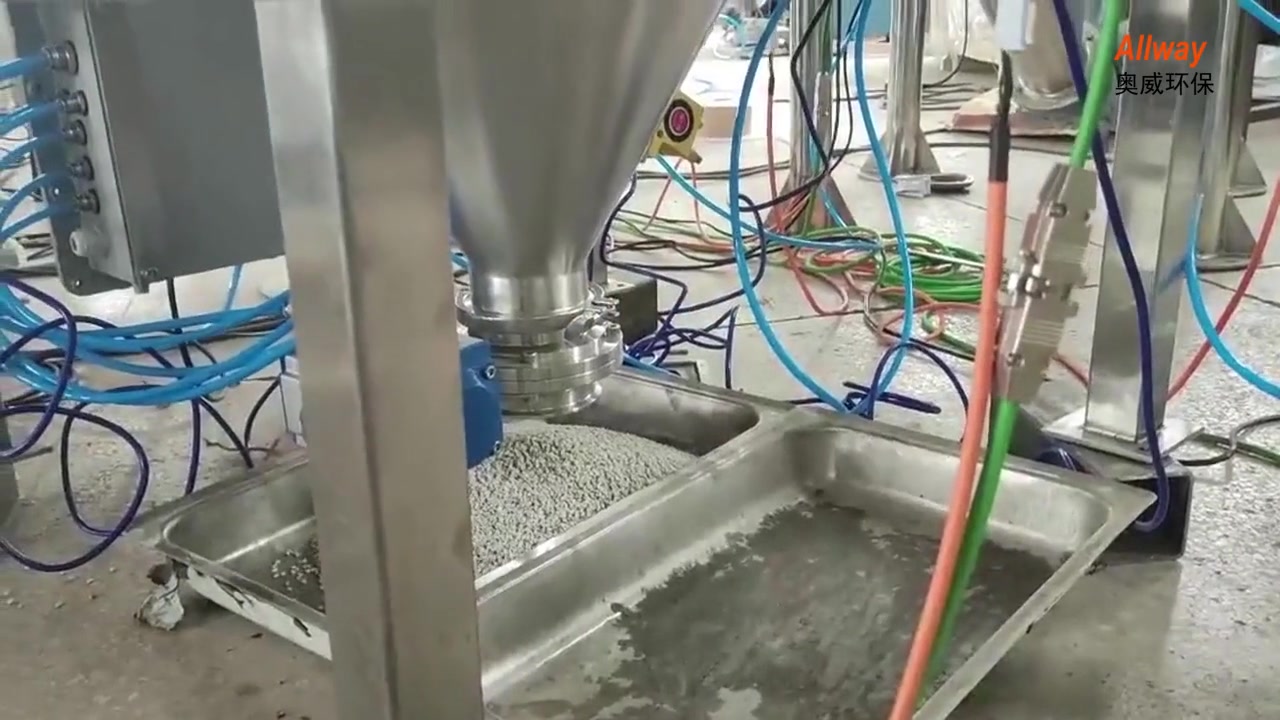
FAQ
Advantages
About Allway

Best bulk bag/sachet unpacking, conveying, mixing, weighing and packaging system Supplier
Large particle material, raw material coarse screening silo
China Vertical screw conveyor manufacturers - Allway
Allway Customized | Packing Machine AWB-Ⅲ
Allway Customized | Packing Machine AWB-Ⅲ
how to install 2 sets of Bulk Bag Unloader for Barbados customer? | Allway
Unpacking machine with broken bags for Xiaoshan, Hangzhou, China - Unpacking and conveying, simultaneous dust removal
Lump crusher for customer in Hunan, China
Automatic control system for vacuum loading and conveying for customer in Beijing, China