New feeding system, rotary component external, completely solve the feeding system susceptible to high temperature steam erosion problem, is a big innovation of the eighth generation of pellet machine;Inside the feeding cover, in addition to the feeding turntable, other non-active parts in contact with materials and steam are all made of stainless steel, which fundamentally solves the corrosion problem of metal materials.
Rice Husk Pellet Processing Technology and Equipment
The most practical use of rice husks is to provide energy as fuel, which is processed into fuel particles by a pellet mill, and burned to generate steam or heat for power generation and heating.

Characteristics and uses of rice husk
The main components of rice husk vary greatly due to different varieties, producing areas and processing methods. Generally, the water content of rice husk is about 12%, 36% carbon, 0.48% nitrogen, 0.32% phosphorus and 0.27% potassium. Rice husk contains about 40% crude fiber (including lignin fiber and cellulose) and about 20% five-carbon sugar polymer (mainly hemicellulose).In addition, about 20% ash and a small amount of crude protein, crude fat and other organic compounds.Rice husk encyclopedia recommended
Usage: rice husk is a good renewable biomass raw material, processed into fuel pellets through pelleting machine, converted into rice husk gas through gasification, direct combustion to generate steam or heat, used for power generation, heating and so on.Rice husk can also produce high quality activated carbon, adsorbent, carbon black, silicon dioxide, silicon carbide, potassium silicate and other chemical products.Rice husk is renewable as a biomass resource compared to oil, gas and coal.In 1971 the Food and Agriculture Organization of the United Nations predicted that the most practical use of rice husks would be to provide energy as fuel.
Husk makes up 20% of the weight of rice.Of the 100 million tons of rice husk produced globally each year, 70 percent is underutilized. Demand is expected to reach 780 million tons by 2022, with even more husks to be processed.Learn more about rice International Rice Research Institute.
The advantages of rice husk pellets
1.After the rice husk is pressed into pellet mill, the volume density is greatly increased, which is convenient for mass transportation and storage.
2.Rice husk pellets burn cleaner.Rice husks leave 15-16% ash when burned before being made into pellets.The ash content after pelleting is only about 6-7%.
3.Rice husk pellets can be fully and efficiently burned with a calorific value of 3200-3500 kcal, which is moderate and suitable for large boilers
4.The rice husk pellet machine has brought economic and social benefits to farmers by transforming rice husk into treasure.
The principle of rice husk pelleting
Pelletizing rice husk is to increase the density of feedstock. Basically, machines that produce pellets could be the ring die (Fig. 1).
Fig. 1. Schematic structure of a ring die-type pelletizing machine.
Rice husk pellets and briquettes have a density of about 500 to 600 kg per cubic meter, 5 times that of their loose form. This increase in density leads to a reduction in transportation cost and increase in the performance of energy conversion processes. The advantages of using rice husk briquettes and pellets recently stimulate a fast growth of these business models in rice production.
Processing technology of rice husk granules
Screening. Removal of impurities in rice husk, such as rock, iron, etc.
Granulation: the treated rice husk is transported to the silo, through which it is transported to the granulator for granulation.
Cooling. After pelleting, the rice husk pellets are at a high temperature and need to be cooled by a cooler to maintain their shape.
Packaging. If you are selling rice husk pellets, you will need a packaging machine to pack rice husk pellets.
Processing technology diagram of rice husk pellets:
Notes in rice husk grain processing:
Rice husk quality is different in different areas and yield is different, so we need to change different ring mold to adapt.Rice husk does not need to be dried, and its water content is about 12%.
1. Before operating the machine, the operator should read the instructions carefully and be familiar with the technological process of the equipment.
2.In the production process, to strict operation rules and sequence operation, and according to its requirements for installation operation.
3. The rice husk granule machine equipment shall be installed and fixed on the horizontal cement floor, and the tightening screws shall be strengthened.
4. Smoking and open fire are strictly prohibited in the production site.
5. After each startup, it is necessary to idle for a few minutes before uniform feeding.
6. It is strictly forbidden to add stone, metal and other hard sundries to the feeding device, so as not to damage the granulation chamber.
7. During the operation of the equipment, it is strictly prohibited to allocate materials by hand or other tools to avoid danger.
8. If there is any abnormal noise in the production process, the power supply should be cut off immediately. After checking and handling the abnormal situation, the machine can continue production.
9. Stop feeding before stopping the machine, and cut off the power supply after the raw material processing of the feeding system is finished.
According to the requirements of correct operation of rice husk pellet machine, and pay attention to relevant matters in accordance with the requirements, not only can improve the output and operation performance of the equipment, but also can prolong the service life of the equipment.
The advantages of high efficiency centrifugal rice husk granule machine are introduced
XGJ560 rice husk grain output: 1.5-2 tons/hour Power: 132 kw Size: weight: 5.4 tons
This is our eighth generation centrifugal high efficiency pellet machine, which is our patented product.It can suppress various types of rice husk with high yield and stable operation.
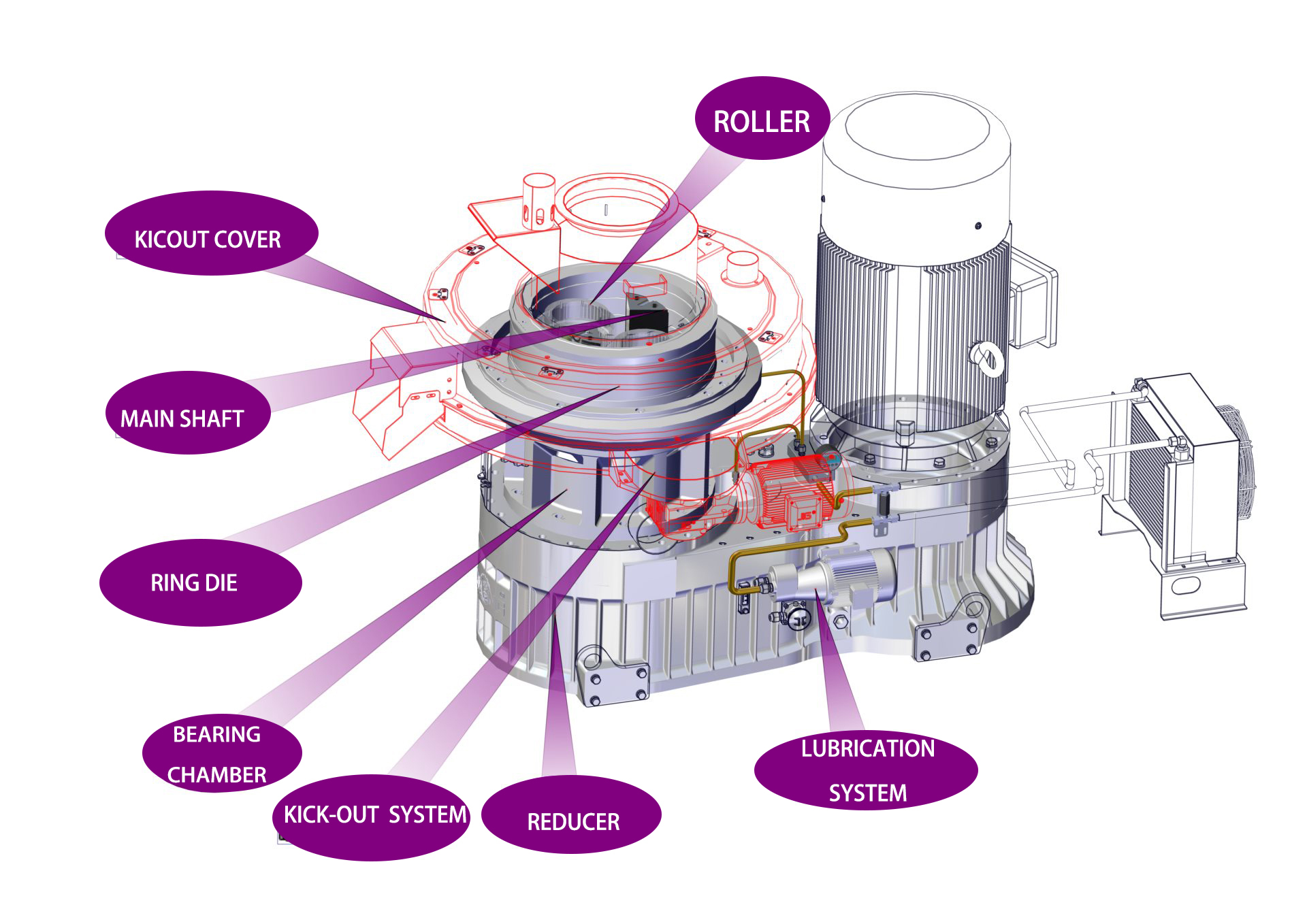
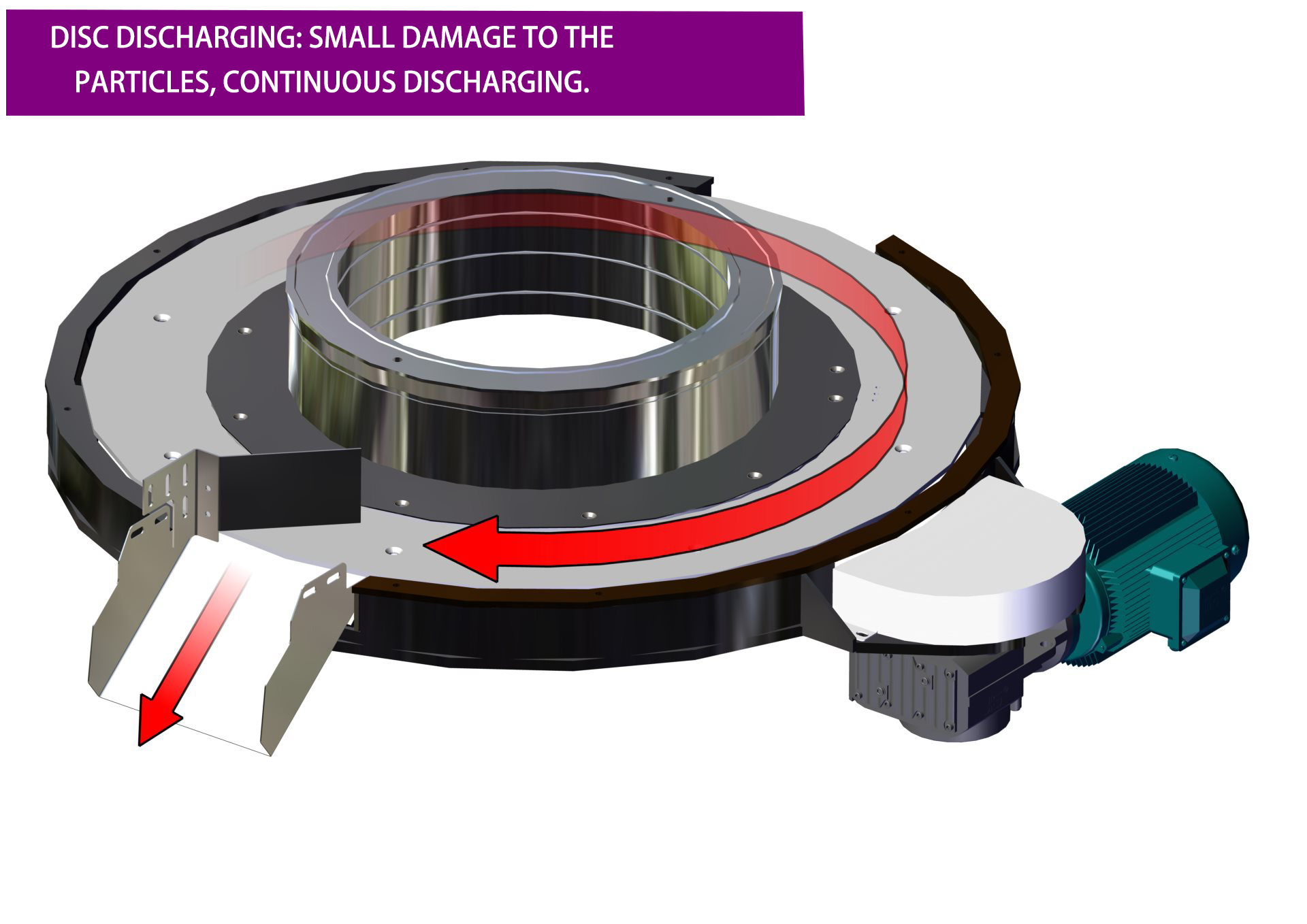
New feeding system, rotary component external, completely solve the feeding system susceptible to high temperature steam erosion problem, is a big innovation of the eighth generation of pellet machine;Inside the feeding cover, in addition to the feeding turntable, other non-active parts in contact with materials and steam are all made of stainless steel, which fundamentally solves the corrosion problem of metal materials.
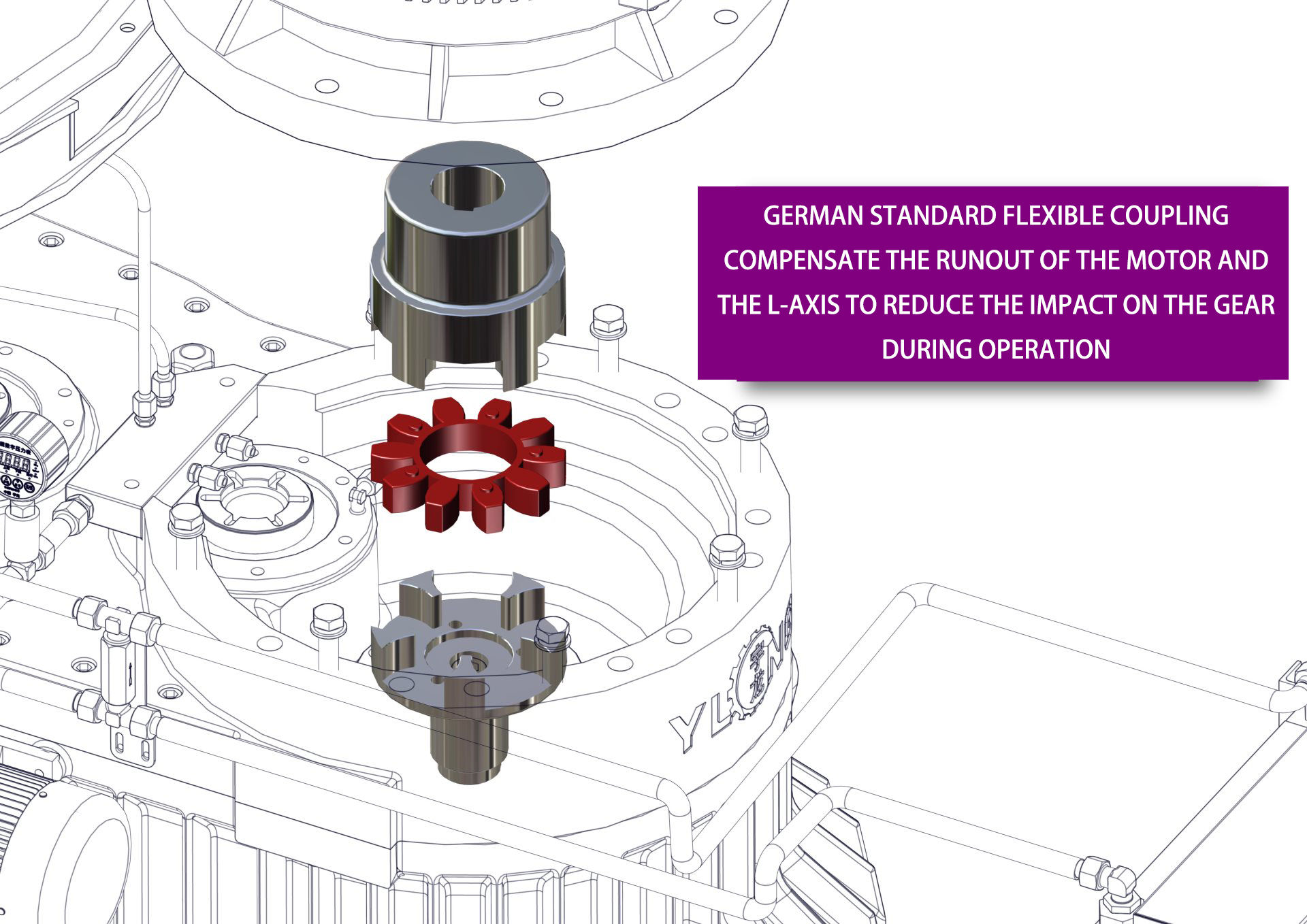
The bearings of the gear shaft at all levels of the gear box are adjustable structure.After the bearing runs and wears out for a long time, it can be adjusted without disassembling the machine, which greatly saves the user's maintenance time.
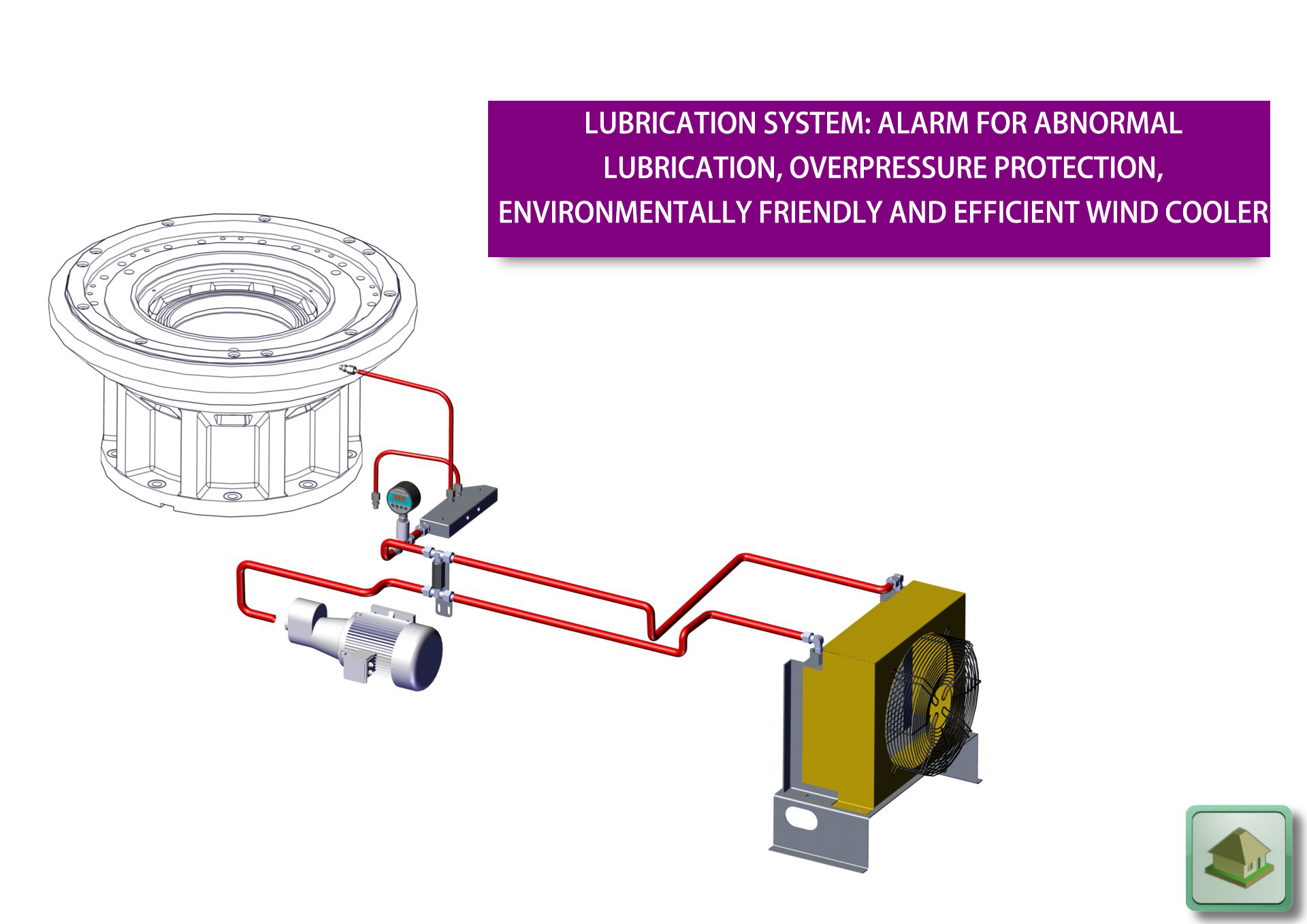
The gear box has its own lubricating cooling system, the machine can realize the cooling of lubricating oil without stopping, to ensure a long time operation.
Real-time lubrication detection, gear box lubrication system is equipped with flow detection and overpressure protection, which can effectively prevent equipment failure caused by poor lubrication.
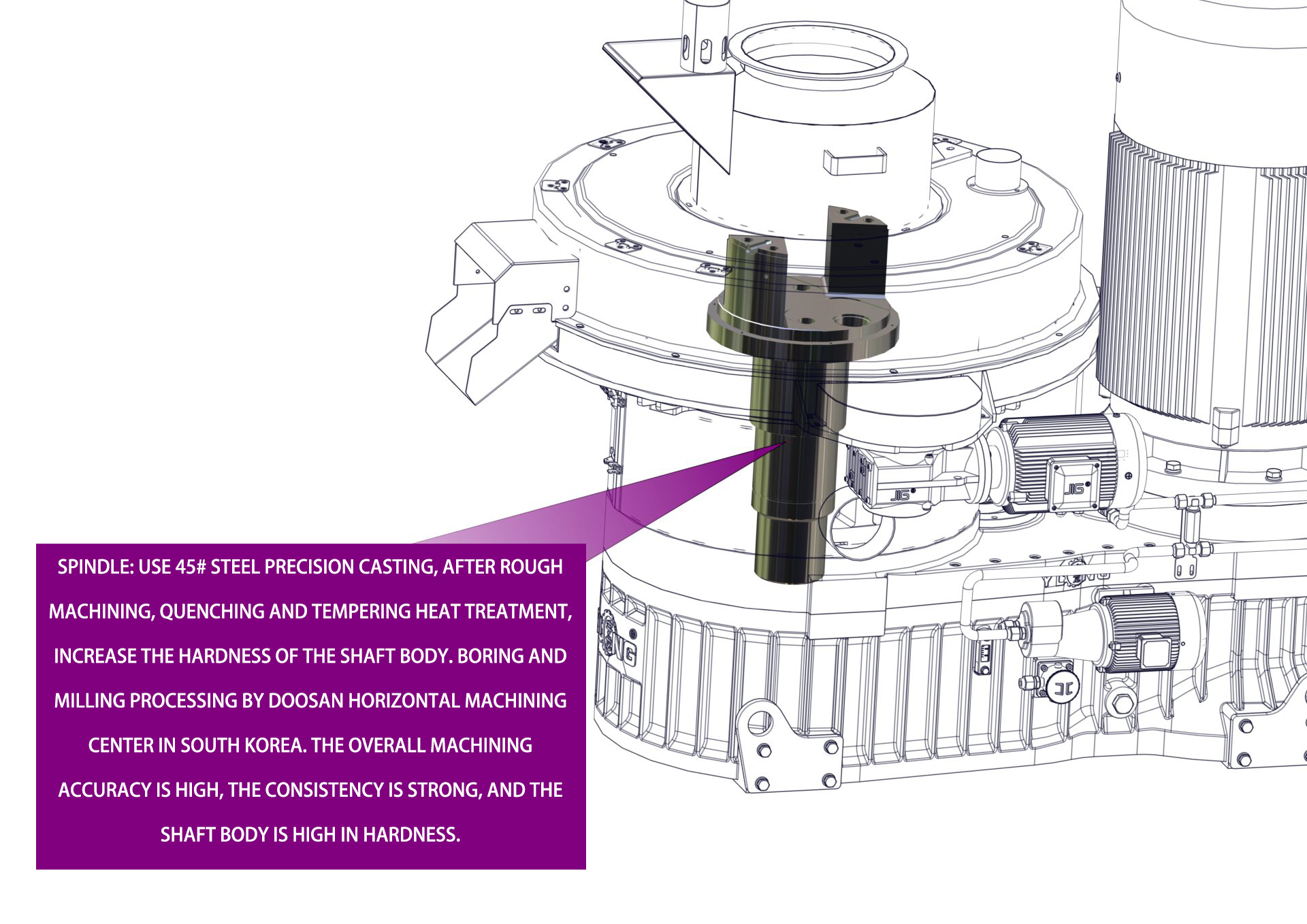
Main shaft: adopt 45 steel precision casting, roughing and tempering heat treatment, increase shaft hardness, Korean Doushan horizontal machining center boring and milling.The whole machining precision is high, the consistency is strong, the shaft body hardness is high.

Making Fuel Pellets From Peanut Shells
Sugarcane Bagasse Pellet Making
Straw for Pellets Fuel Production
Rice Husk Pellet Processing Technology and Equipment
How to Assemble Pellet Machine / Pellet Machine Installation - Detailed Guide [2022]
How to Assemble Pellet Machine / Pellet Machine Installation - Detailed Guide [2022]
Making Fuel Pellets From Peanut Shells
YULONG 8th Generation Centrifugal High Efficient Pellet Machine
Activated Carbon Granulation