JK2M2283 Nema 42 / 52 Stepper Motor Driver
Product Type: Nema42 52 Stepper Motor Driver
Feature summary:Low heat generation, low motor vibration and stable operation, Smooth operation and low noise
Place of Origin:china
Minimum order quantity:10pcs
Support Motor: Nema42 or Nema 52 Hybrid 2 Phase Stepper Motor
Packing:The sample is packed in carton,the batch with plastic pallet
Delivery time:Standard product: 7-10days
Customized product: 25-30days
Transaction mode:EXW, FOB, FCA, CIF, FAS, CFR, CPT, CIP, DAF, DEQ, DDU, DDP...

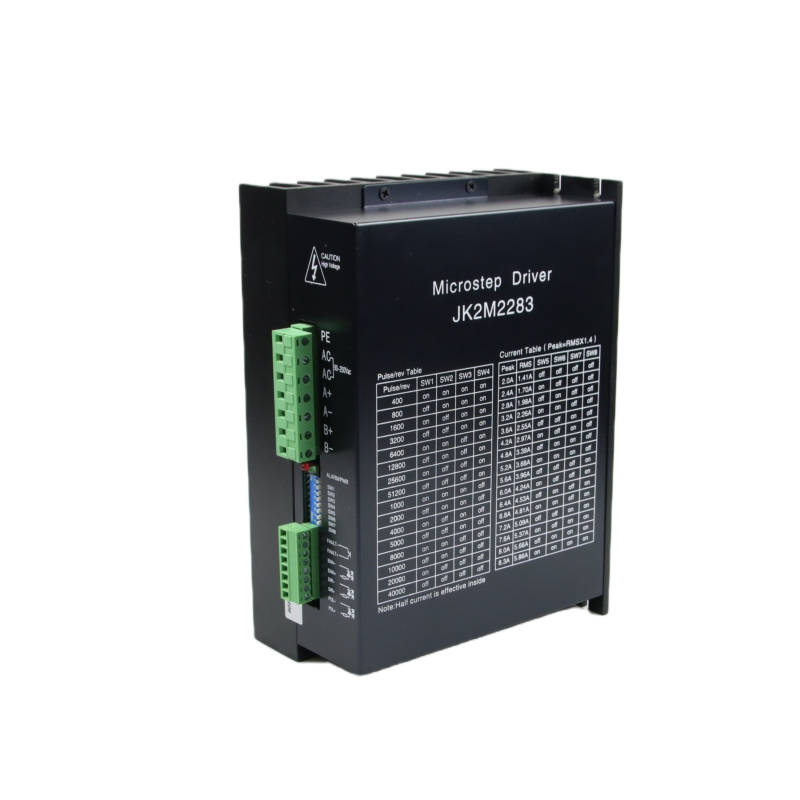
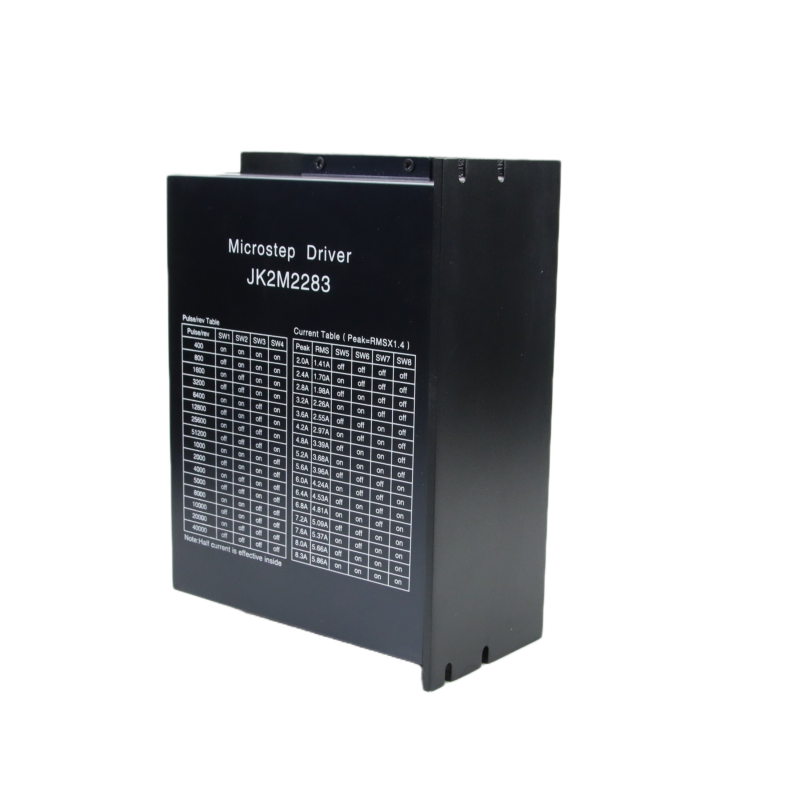
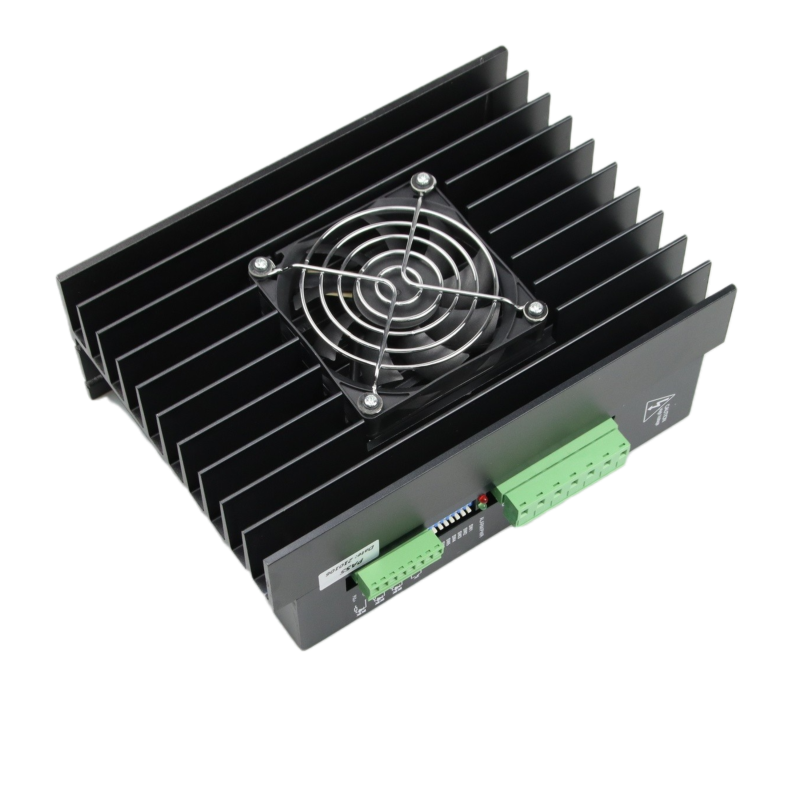
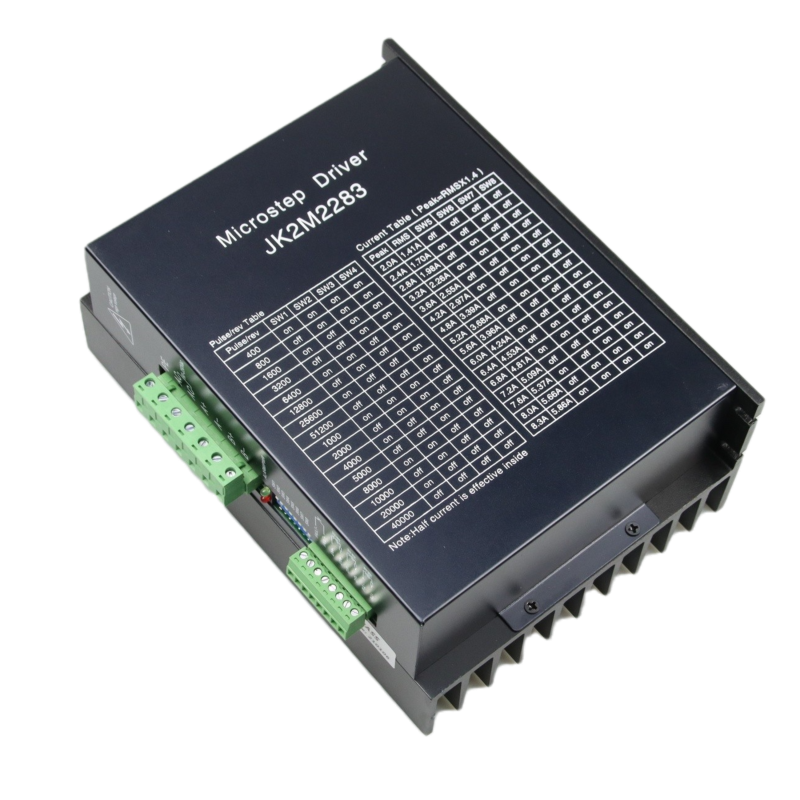
Features
● High-performance, low price
● micro-step
● Automatic idle-current reduction
● Optical isolating signal I/O
● Max response frequency up to 200Kpps
● Low temperature rise, smooth motion
● Online adaptive PID technology
Overviews:
JK2M2283 is subdivided and high-performance stepper motor drive using constant angle and constant torque,which is designed for 130BYG、110BYG and other 8A following two-phase, four-phase hybrid stepping motor. The driver uses the circuit which is Similar to the principle of servo control with the features of smooth running, low noise, low vibration, low temperature rise of the motor .It has 16 kinds of micro-step, and the micro-step can be set from full step to 51200steps/rev.The working current can be set from 2.0A to 8.3A, and the output current has 16 stalls, the current resolution is about 0.5A; with automatic semi-flow, self-test, overvoltage, under-voltage and over-current protection. This driver is AC power, Voltage does not exceed 240VAC not less than 120VAC.
Applications
Suitable for a variety of large-scale automation equipments and instruments. For example: labeling machine, cutting machine, packaging machine, plotter, engraving machine, CNC machine tools and so on. It always performs well when applied for equipment which requires for low-vibration, low-noise, high-precision and high-velocity.
Parameter | Min | Typical | Max | Unit |
Input Voltage(AC) | 150 | - | 220 | VAC |
Output current | 0 | - | 8.3 | A |
Pulse Signal Frequency | 0 | - | 200 | KHZ |
Logic Signal Current | 7 | 10 | 16 | MA |
1) Current setting: Dial switch:ON=0;OFF=1
Phase current | SW5 | SW6 | SW7 | SW8 |
2.0 | 1 | 1 | 1 | 1 |
2.4 | 0 | 1 | 1 | 1 |
2.8 | 1 | 0 | 1 | 1 |
3.2 | 0 | 0 | 1 | 1 |
3.6 | 1 | 1 | 0 | 1 |
4.2 | 0 | 1 | 0 | 1 |
4.8 | 1 | 0 | 0 | 1 |
5.2 | 0 | 0 | 0 | 1 |
5.6 | 1 | 1 | 1 | 0 |
6.0 | 0 | 1 | 1 | 0 |
6.4 | 1 | 0 | 1 | 0 |
6.8 | 0 | 0 | 1 | 0 |
7.2 | 1 | 1 | 0 | 0 |
7.6 | 0 | 1 | 0 | 0 |
8.0 | 1 | 0 | 0 | 0 |
8.3 | 0 | 0 | 0 | 0 |
2) Micro-step Setting: Dial switch:ON=0;OFF=1
Subdivision | SW1 | SW2 | SW3 | SW4 |
400 | 0 | 0 | 0 | 0 |
800 | 1 | 0 | 0 | 0 |
1600 | 0 | 1 | 0 | 0 |
3200 | 1 | 1 | 0 | 0 |
6400 | 0 | 0 | 1 | 0 |
12800 | 1 | 0 | 1 | 0 |
25600 | 0 | 1 | 1 | 0 |
51200 | 1 | 1 | 1 | 0 |
1000 | 0 | 0 | 0 | 1 |
2000 | 1 | 0 | 0 | 1 |
4000 | 0 | 1 | 0 | 1 |
5000 | 1 | 1 | 0 | 1 |
8000 | 0 | 0 | 1 | 1 |
10000 | 1 | 0 | 1 | 1 |
20000 | 0 | 1 | 1 | 1 |
50000 | 1 | 1 | 1 | 1 |
3) Control signal Connector:
signal | function |
FAULT- | Common anode input positive terminal |
FAULT+ | |
ENA- | Enable signal terminal motor is offline when Enable signal is active, no internal current. |
ENA+ | |
DIR- | Direction signal terminal Direction control signal control the motor running direction. |
DIR+ | |
PUL- | Pulse signal terminal Pulse signal control the motor to run motor run 1 step after each pulse. |
PUL+ |
4) Power and Motor Connector
AC | Power supply, 150~220VAC |
AC |
|
A+ | Motor phase A |
A- |
|
B+ | Motor phase B |
B- |
5) Problems and Solutions
Phenomenon | Possible Cause | Solutions |
Fault indicator brightens red for a long time (over-current) | Electrical wire shorted | Check the motor lines and eliminate short circuit |
| Motor failure | Replace motor |
| Other reasons | Check back |
1、Q: Are you factory?
A:Yes, we are factory, and we produce stepper motor/driver, Servo motor/driver, BLDC motor/driver...
2、Q: How to select models?
A:Before purchasing, please contact us to confirm model No. and specifications to avoid any misunderstanding.
3、Q: How do you ship the goods?
A: Sea and by air, also accept customer appointed.
4、Q: Can I test sample?
A: Yes, sample charged can be offered for testing.
5、Q: Can we be agent or distributor?
A: Yes, welcome and we will support you.
6、Q: Can you do OEM or ODM service?
A: Yes, we have R&D department and accept OEM and ODM service.

1.8°Nema 34 Linear Stepper Motor 86x86mm for for 3D printer CNC Engraving Milling Machine
1.8° Nema 14 Hybrid Stepper Motor 35x35mm 0.5A or 1A with 4leads
1.8° Nema 34 Hybrid Stepper Motor 86x86mm with 4leads or 6leads
1.8° Nema 16 Hybrid Stepper Motor 39x39mm with 4leads or 6leads
1.8 Degree Nema 11 Hybrid Stepper Motor 28x28mm 0.67A or 0.95A With 4leads or 6leads
0.9° 36mm 2-Phase Hybrid Round Stepper Motor 36x36mm With 4leads
1.8° Nema 24 Worm Gearbox Stepper Motor 60x60mm for CNC Milling
1.8° Nema 24 HSG Eccentric Gearbox Stepper Motor 60x60mm for CNC Milling
1.8° Nema 24 HSP Planetary Gearbox Stepper Motor 60x60mm for CNC Milling